3D Bio Printing hardware and processes designed specifically for researchers
Jimmi Bio Printer and positive pressure sterile glove box, equipped for liquid collagen printing
We’ve already seen how 3D Printing is beginning to have a transformative effect on the global manufacturing industry, and soon, we see the same thing happening with 3D Bioprinting. 3D Bioprinting will have a transformative effect on medicine, agriculture, and biofabrication. But here’s the thing: at a time when the interest in and potential for 3D Bioprinting is very high, there is a demand for accessible bioprinting hardware and educational resources that has not yet been met.
The Jimmi bio printing venture designs and builds 3D bioprinting hardware for researchers in regenerative medicine, and provides educational products to help integrate the these new tools into research. We are currently in the pre-launch product development process, developing hardware, printing procedures, and instructional content.
Recently there has been some interesting work underway printing alginate via the F.R.E.S.H method and we have developed some new, low-cost hardware for printing liquid collagen.
Tools and Processes:
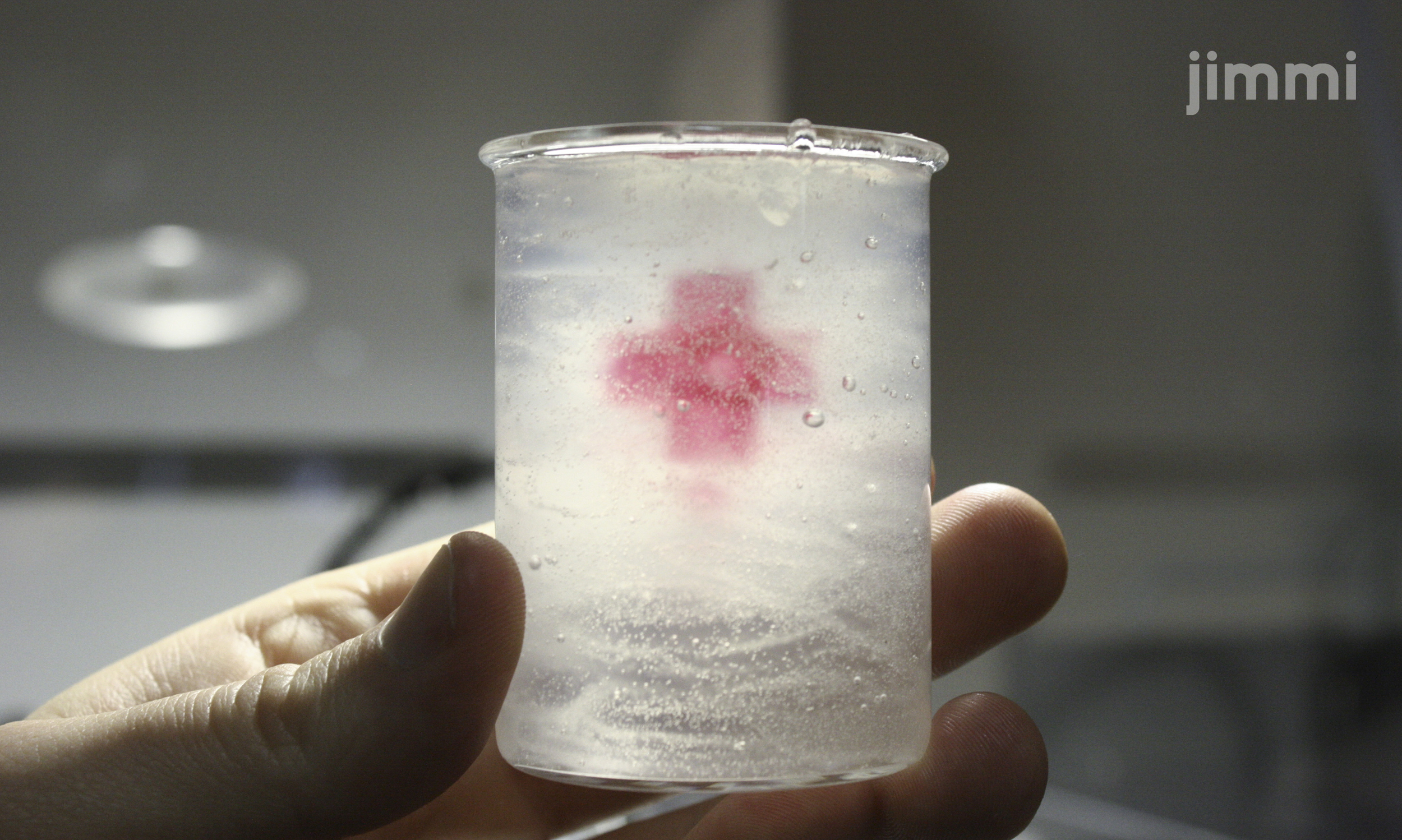
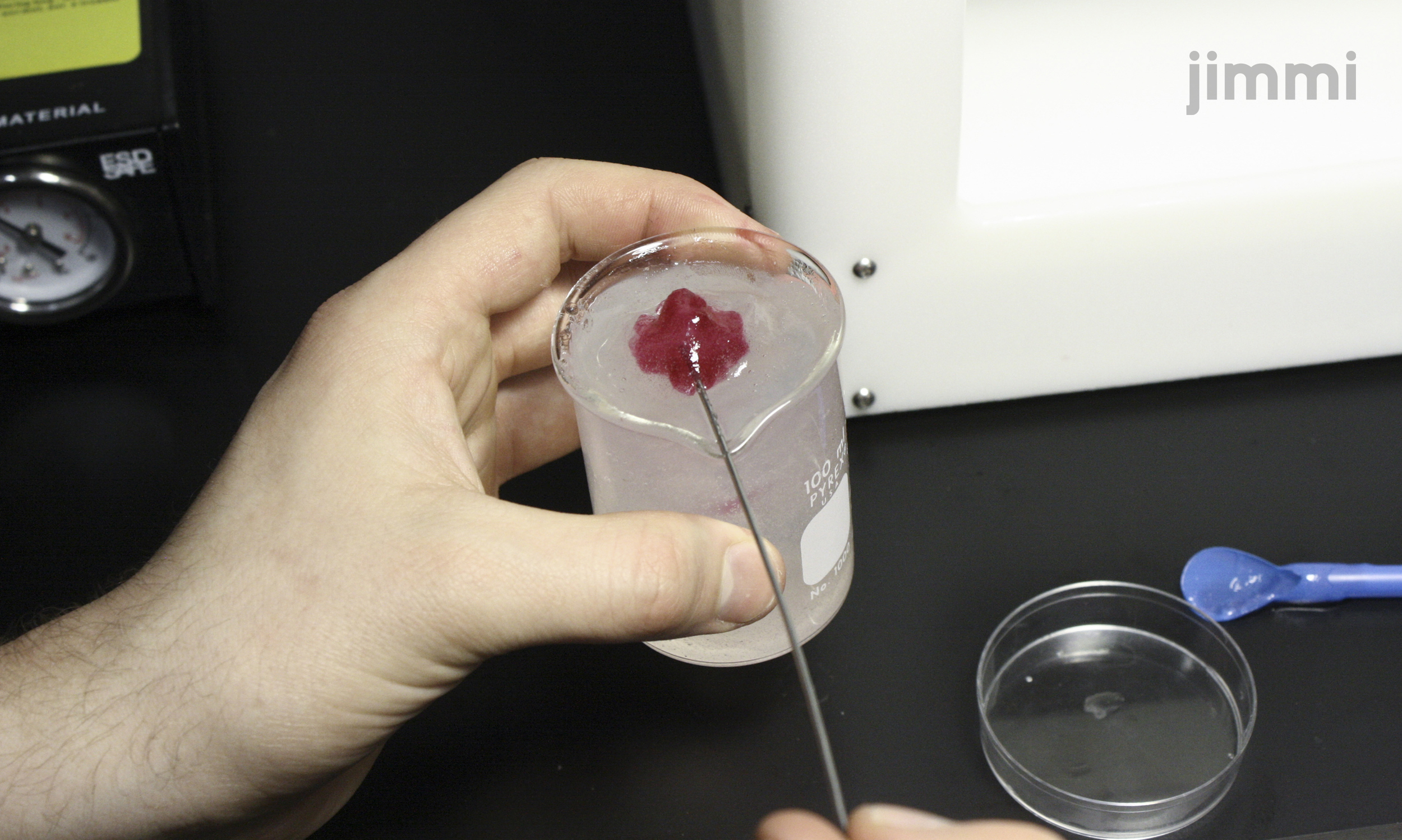
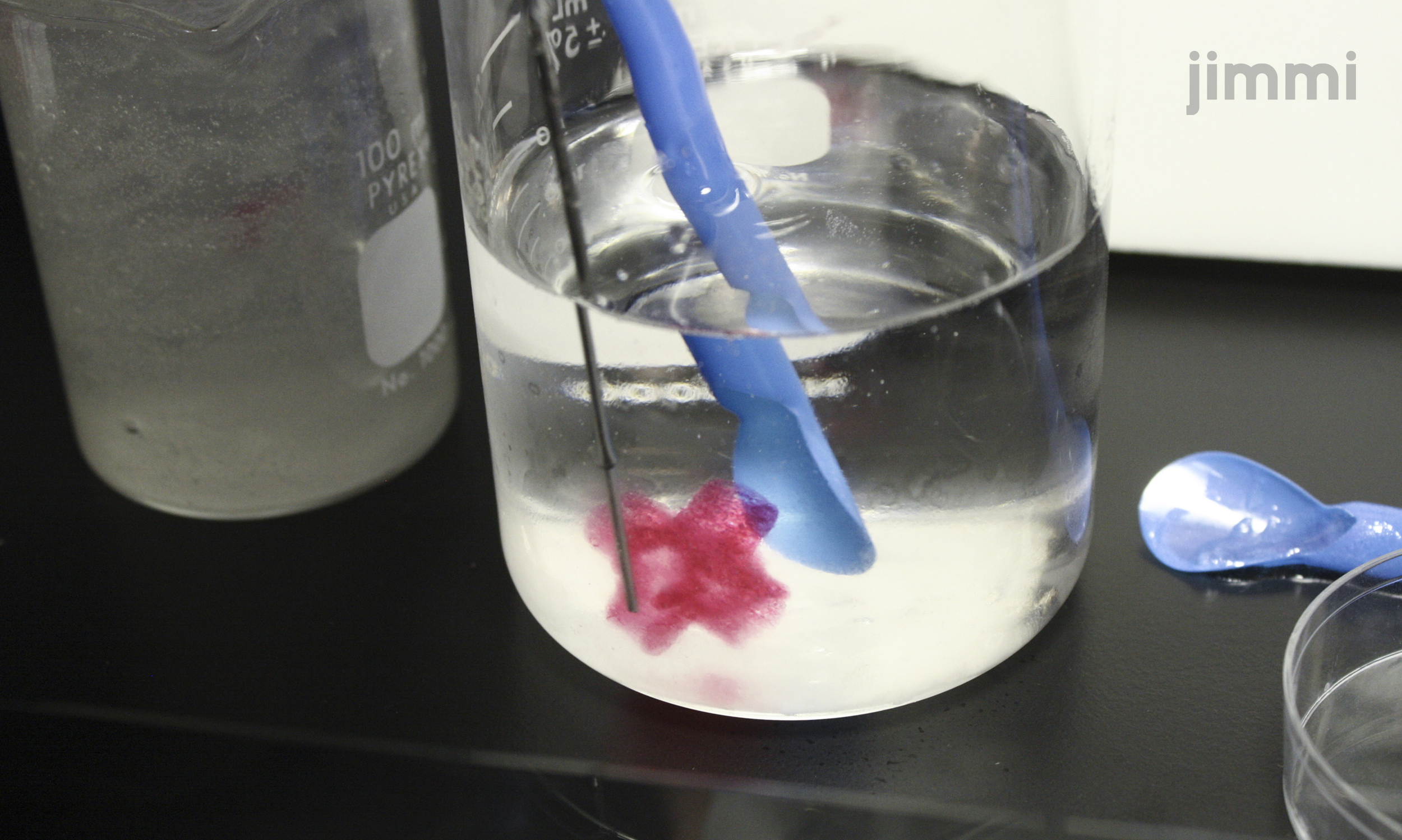
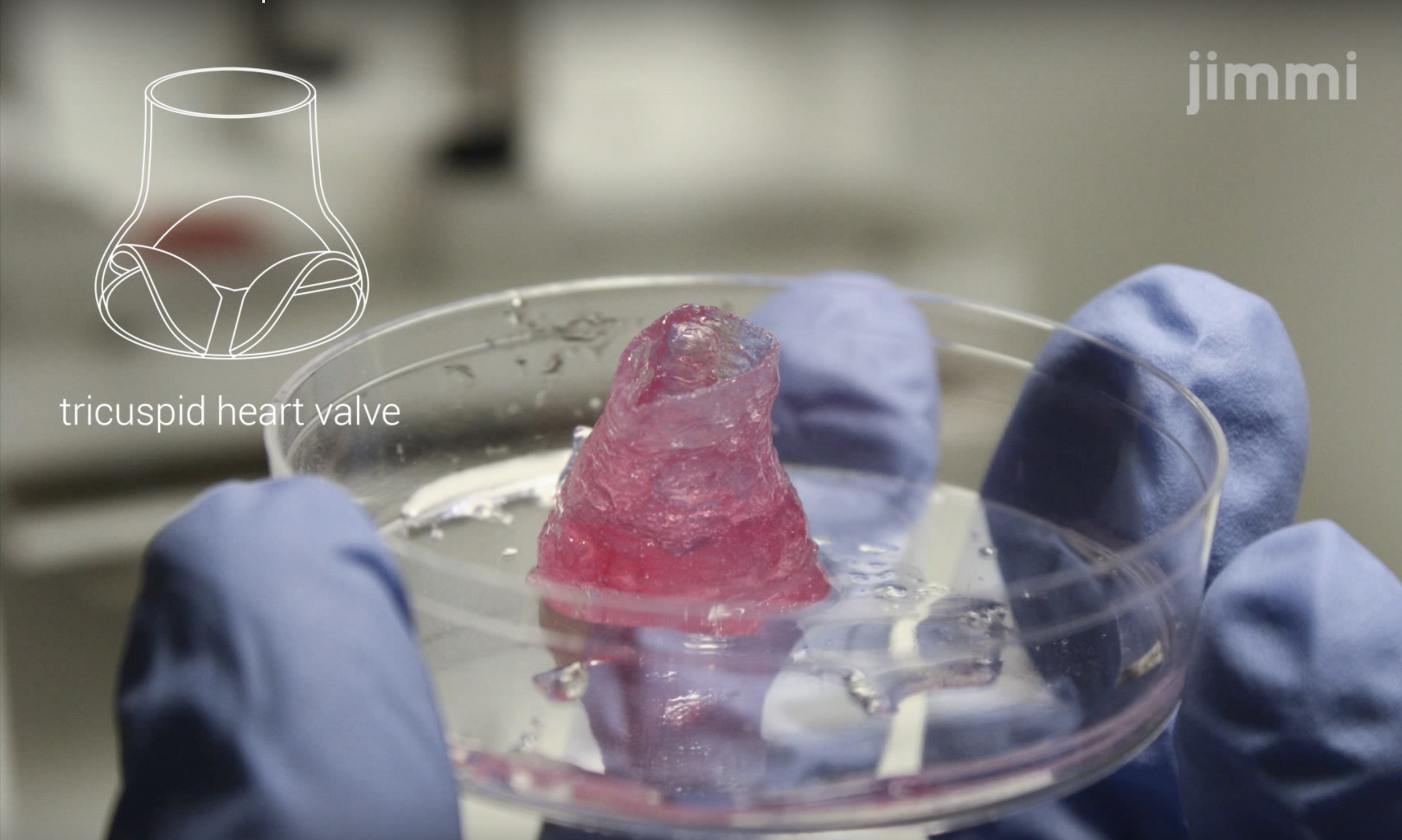
Chilled Collagen Toolhead
We are heading development of a thermoelectric cooler/heater collagen extruder for Guenther Lab at the University of Toronto for printing liquid collagen.
The hypothesis is that printing with liquid collagen will allow for a higher level of control over print parameters and detail. Additionally, rather than printing with gelled collagen, printing in liquid collagen might create a more homogenous and stronger print as the entire volume of the print will crosslink together in post processing. Collagen begins crosslinking at room temperature and needs to be stored at 4c to prevent crosslinkage and maintain a liquid form. We are attempting to print with liquid collagen via a Pneumatic syringe dispenser with a chilling unit to cool syringe to a constant 4c.
We are controlling temperature with a Peltier Element. This is a really interesting part because it can product temperatures as low as -12c and as high as +100c, making a toolhead that is extremely versatile for printing many types of biomaterials at either cool or warm temperatures.
Above: early works-like prototype of the chilling block.
Below: video outlining the system of the chilling block installed on the 3D printer and cooled to ~4c.
Moving from the works-like prototype to a manufacturable part:
The prototype (1) was built from laminated aluminum slices cut on a CNC router, we used this same method to make a more refined version with full syringe body contact (2). To make a production quality part, we used a Haas VF1 machining center to mill the part from a solid block of aluminum (3). This version conducts heat more efficiently and has tighter meshing faces for the syringe body and thermocouple, making for more efficient and precise cooling.